SLA Resin printers are a powerful tool that can print in greater detail than conventional FDM printers can and use a stronger material. However, they are slower, trickier, and more dangerous to use. Formlabs has a fantastic website where you can read more in depth about the nuances of their machines. Resin is a material that sits in a tank as liquid but cures (solidifies) when exposed to ultraviolet light. The resin printer projects UV light at a bath of resin to cure it in layers, drawing your piece out of the bath layer by layer.
The EXPmaker has two Formlabs Form 3L SLA Printers available for use, and they each have a build volume of 33.5 × 20.0 × 30 cm (13.2 × 7.9 × 11.8 in). A print on one of these resin printers takes at least twice as long as doing the same print on an Ultimaker, and post-processing will take at least 45 minutes.
Safety Considerations
Printer Anatomy
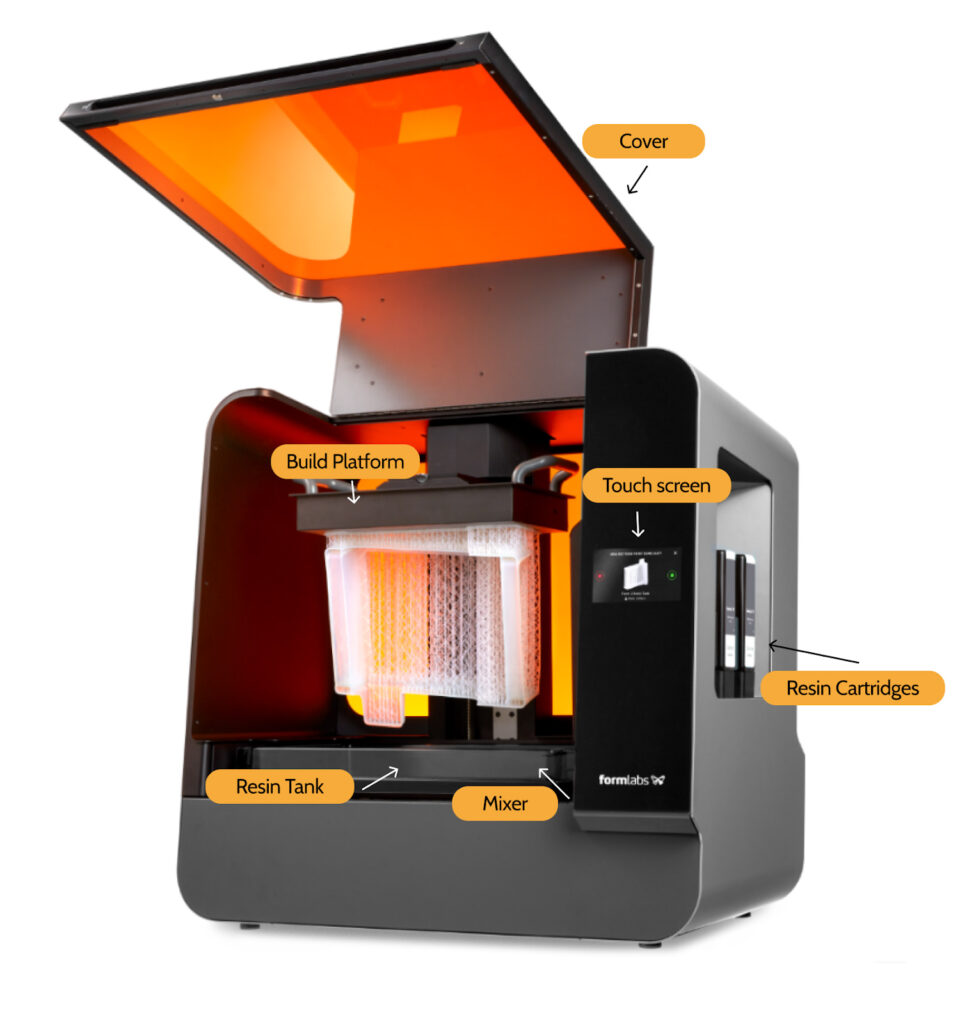
Software Download
PreForm, the free slicer software for FormLabs, can be downloaded here. The workstations in the 3D printing room will have this software pre-installed, but you can also download it on your personal computer if you wanted to set up your part outside of EXPmaker.
Operating the Machine
Load your part into PreForm:
PreForm is a “slicer” software, so called because it slices a digital 3D model into layers so that the printer can build it up. In this case, the model is an STL file.
- Open PreForm from the desktop. Choose the right printer settings now (you can change this later, but it’s more work).
- Pick a layer thickness. The thicker the layers, the faster the print, but the lower the resolution will be. Generally, very small parts, or parts where you need dimensional accuracy to be within 1mm of what you’ve printed, will require a smaller layer thickness.
- The longer your print, the more expensive it will be and the more likely it is to fail! 0.025 micron resolution will take dramatically longer than 0.1 micron resolution. Most of the time, you do NOT need to have a small layer thickness. Make sure to check with an Explorer if you want to print in high resolution to make sure it’s appropriate for your application.
- Form 3 printers have a cool beta feature called “adaptive layer thickness”, where the software will choose parts of your print to be high-resolution and parts to be low-resolution. This is still a beta feature, so we don’t recommend it. Check with the makerspace technician if you’re interested in trying it out.
- Keep print settings as default.
- Under “File,” click “Open” and open the STL file you want to print. It will appear in the print window, showing you the piece in relation to the print bed.
- If you have multiple pieces you want to print, open them each. The first will appear in the center of the bed; the rest will appear around it.
Format your print
On the right-hand side of the screen is a column of buttons. You will use these controls to arrange and set up your print by clicking the part you want to adjust and then clicking one of these. From top to bottom, they are arranged in the order in which you should use them.
- The first tool is the Magic Wand, which offers One-Click Print. This is one of the most useful tools: when you click it, Pre-Form will automatically move your part to what it thinks is the best print position. The software is intelligent and will consider the print size and the angle to which it is best suited.
- The next button is Size. You can use this to scale your parts uniformly by choosing a scaling factor or selecting the part length along one axis.
- General best practice in 3D printing is to scale or resize your models OUTSIDE of a slicer software, so it’s recommended that you don’t touch this.
- Below the magic wand is the Orientation tool, which lets you rotate your pieces. Print angle is essential on the resin printer since it determines how long your print will take and the chance it will succeed. Unlike traditional FDM pieces where the flattest part should be on the print bed, Formlabs printers work best when prints are ANGLED. The main thing to consider with orientation is splitting and merging pieces. A piece that begins as one part and branches out is more likely to succeed than a piece that begins as two pieces that must then be fused.
- Beneath that is the Supports tool. Supports are the scaffolding that supports your piece while it prints, but that are broken off when the print is done. The supports will auto-generate when you click “Generate All.” You should NEVER print directly on the print bed/print without supports and a raft.
- As in all 3D printing, you don’t want supports on important features or surfaces. If supports generate on top of important features on your print, you can manually remove or add supports. Preform is smart– it’ll tell you where you need to add supports.
- Please make sure that “Raft Label” is checked; this will make it easier to locate your print if it gets lost.
- Internal supports are supports inside your print. These are necessary if your print has any hollow parts (your print will fail if you try to exclude them). Try to adjust orientation of your prints to minimize the amount of internal supports, as they are very difficult to remove in post processing.
- There are other settings you can experiment with, including raft type and touchpoint density. We recommend keeping these as a default.
- The last tool to use is Layout. This lets you move the pieces around the bed, so you can ensure they do not overlap.
- You should also use this tool to pull your details closer to the “mixer side” side of the plate, as indicated in the software. This helps with the print’s reliability, but it might not be possible with larger pieces. Move the piece over if possible, but don’t compromise the rest of the layout rules to achieve this.
- The Form 3L is different from some other Form machines because there are TWO lasers that enable printing; one for each side of the bed. You can see this where it says “laser seamline”. If you put a part here, it will have a literal seamline (similar to flashing in injection molded parts). With large prints, sometimes it’s unavoidable to cross this seamline. With smaller prints, you should avoid putting things over this line.
- You can also duplicate the amount of parts that you have here, if you’re printing multiple parts. Make sure to duplicate AFTER you’ve refined your supports/orientation. This saves you time, since the supports/orientation will duplicate as well.
- Note on the right side of the screen two sections: Details and Printability.
- Details will show you printing time, the number or layers, and how much resin you’re using. The print time and the amount of resin used will be used to calculate how much money your print will cost. You will not be charged for post processing time, but please remember that you MUST post process a print for it to be usable. Post processing will take at least another hour.
- Printability should read “pass”. Minima and cups are the types of places where your print is most likely to fail (it might not and you can still print anyway, but chances are it will fail).
Send your part to the printer.
- When you have used these five tools, click the yellow “Print” button. A window with a few options will come up. Check the printers to see if they’re in use; if one is, you should choose the other. You will also see two indicators of the resin levels, one for the resin in the Resin Tank and one for the resin in the Cartridge.
- When you print, check the level in the cartridge, shown in the icon in the print window. If it is full or mostly full, you’re all set. If it is half full or less, you can probably still print, but show the resin level to an Explorer. If there isn’t enough resin, what will most likely happen is that you will start the print, and the Explorers will swap out the cartridge when it runs out. The resin printer can keep running for a few minutes with just the resin in the bed, which means the cartridge can be changed while the machine runs.
- Finally, you can name your job, formatted as Last Name, First Initial: whatever your print job name is (for example: Aoun, J: Husky V2.4). and click “Upload Print.” This will send the file to the resin printer you selected.
Set up the physical machine
- Go to your printer. You should see the job you sent on the printer’s display screen. A “Print Now” button will be in the lower right corner, and press it on the touch screen. One of two things will happen.
- If the printer believes it is ready, it will start heating up for your print. It will indicate the printer’s current temperature and the temperature at which it will begin printing. There is a “Start Now” button; DO NOT push it. This will force the print to start at a colder temperature than it should, and it will be very likely to fail. Let the printer heat up and start on its own time.
- If the printer doesn’t believe it is ready, it will display the problem. Usually, this will be either a message about the cartridge or the bed level. In either case, tell an Explorer. They can help you swap out the cartridge, level the printer, or make other adjustments. Once you’ve done that, it should start heating up and preparing to print.
Retrieving your print
- The screen on the resin printer will tell you how long the print will take. Unlike an FDM printer, you cannot retrieve your piece when this time is up since it will still be covered in caustic uncured resin. Instead, it must be removed from the printer by an Explorer. The piece will then be put in the isopropanol bath to wash the uncured resin off, then baked in a curing oven to fully solidify it. This process will take an additional 30 minutes to an hour.
- When you start a print, let an Explorer know when it will be done so that they can remove and cure it when it is time. You can also come back when your part is done and have an Explorer train you on using the bath and curing oven so that you can process your pieces in the future.
- You do not want your print to finish at a time when nobody can retrieve it for a long time (more than 12 hours, such as right before a holiday or weekend). This is because Formlabs printers are not designed to have parts hanging for extended periods of time and since leaving uncured resin on your part for a while may affect the integrity of your part.
Post-Processing your print
There are two steps to post-processing a print. First, it must be bathed in isopropanol alcohol to wash off any liquid resin. Then, it must be cured to solidify the resin fully. (While you technically can skip the curing process, your part will be dramatically weaker than what it’s supposed to be and it’ll also be very, very gross. Please talk to the makerspace technician if you are curious about skipping curing.)
Washing the Part
The wash is a tank of isopropanol (IPA) that removes uncured (liquid) resin from your part. Your part will be covered in uncured resin as you handle it, so always wear gloves!
- First, check and prepare the wash. The two things you’re checking for are IPA level and saturation. For the level, look at the front of the tank. There are two black lines towards the top: the liquid must come up somewhere between these lines. A bit of it gets used up each time a part is washed so that the waterline will go down. If it is below the lower line, tell an Explorer, and they will refill the tank.
- Lift the orange lid of the resin printer. On top of the bed, there is a small lever. Lift it and slide the entire bed forwards to remove it. Lower the lever and close the lid, so the resin isn’t exposed to ambient light.
- Using the control dial on the wash, select “Open.” The lid will open, and the basket will rise. Place the print bed with your part on the rack, so the part is above the basket.
- Using the control dial again, select “Start.” The basket and part will lower into the IPA, close the lid, and begin a ten-minute wash process. Wait until it is done.
Best practices for cleaning
- Any small features that need to be preserved should be cleaned now. While the wash gets off most of the resin, there might be small amounts of resin left on your part. Things such as small holes, which may have resin stuck inside them, will cure shut if you don’t clean them out at this step.
- To do this, you can use pins, compressed air, and squirt bottles of IPA. Make sure to clean up afterwards.
- If you wipe up resin and IPA off the table or your part, your gloves and paper towels MUST go into a hazardous waste “mayo jar”, which should always be contained into another, bigger bin. Do NOT dispose of anything in the trash. Dirty pins must go into a sharps container. If anything is full, please tell an Explorer.
- If you need to thread any holes in your part, now is the time to do so! Doing this after curing may splinter the part. Ask the makerspace technician for help if this is applicable to you.
Curing the Part
- When the wash is done, the machine will automatically open and raise the part out of the IPA. It’s important to note that the part will still be wet with IPA. If it is left to sit too long before curing, parts of it may dissolve.
- Remove the bed from the rack on the wash. Wearing gloves and using a scraper, carefully remove your print from the bed. Try your best not to scrape the print bed with the scrapers; the more scratched up a print bed is, the more difficult it will be for future parts to adhere to it.
- Use the wash’s control dial to select “Sleep,” which will close the machine, so the IPA doesn’t evaporate.
- Open the lid of the curing oven. Place your part on the turntable. If it is a long part, ensure it won’t reach past the rim of the turntable. Close the lid and, using the control dial, select “Start.” The machine will first heat up to 60℃ and display the temperature on the screen.
- Once it reaches the correct temperature, it will rotate the turntable and shine ultraviolet light on your part, which will look purple. This process will take half an hour. You don’t have to wait around while it happens, but your part is ready to go once it is done.
- Now that your part is fully cured, you can remove it from the curing oven. You won’t need gloves anymore as long as it’s fully dry! If any parts of it still look wet or shiny, some of the resin may not have been cured: put it back in the curing oven and run it for another five to ten minutes OR clean out the resin with the IPA squirt bottle or the compressed air before putting it back in the oven (best if resin is stuck on essential features). This choice is up to the user. Resin won’t be harmed by curing it too much, so you can keep curing it until it is completely dry.
Finishing the part
- Once the part is completed, use snips to cut off the supports. You MUST wear safety glasses while doing this, since the supports have a tendency to go flying when you cut them off.
- Since the supports and raft are cured, you may throw these parts in the trash instead of the hazardous waste mayo jars.
- Sandpaper or dremels can easily be used to sand off any remaining bits of support material, or to smooth out the “steps” from layers.